Automatic batching and control system of internal mixer the system is mainly composed of feeding system, storage system, weighing system, mixing system, conveying system, etc. the carbon black weighing system can reduce the crushing of carbon black caused by conveying. The bag filter can effectively control the flying of carbon black. The weighing system can complete the weighing and feeding of carbon black, oil and rubber. The system has the functions of computer control, including raw material management, formula management, work order management, user authority management, weighing batch data report, real-time and historical alarm, online monitoring, etc.
It has the following advantages and characteristics:
1. High measurement accuracy can ensure product quality
2. The main material weighing range is 10-1000kg, with an accuracy of ± 200g or ± 0.5%; the auxiliary material weighing range is 200g-50kg, with an accuracy of ± 50g or ± 0.5%; the liquid weighing range is 1kg-200kg, with an accuracy of ± 20g or ± 0.5%.
3. Adopt 304 stainless steel and imported brand parts, stable and durable.
4. The important parts of the equipment and all parts in contact with the raw materials (such as raw material storage barrel, dust collection device, transmission pipeline, metering bucket, etc.) are made of 304 stainless steel, with strong corrosion resistance and long service life of the equipment; knife gate valve, fan, etc. are all imported from Taiwan, and other important parts are also made of domestic or international famous brands to ensure stable, reliable and durable operation of the equipment.
5. Negative pressure mode is adopted for raw materials to effectively reduce workshop dust and use cost.
6. The raw material area can be isolated from the production line, which can not only effectively reduce the dust concentration in the workshop, but also save the cost of handling raw materials; the system occupies a small space, and can be installed in the first or second floor workshop, which helps to reduce the construction cost.
7. Error prevention control to help reduce additional losses.
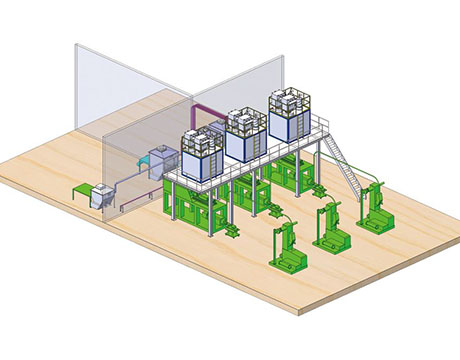